The Reztsoff metal structure plant operates a certified laboratory of nondestructive inspection (LLC “Master-Class”), which produces incoming, operational and acceptance control of equipment and materials during the manufacture of metal structures. Certified laboratory specialists conduct technical diagnostics by nondestructive methods.
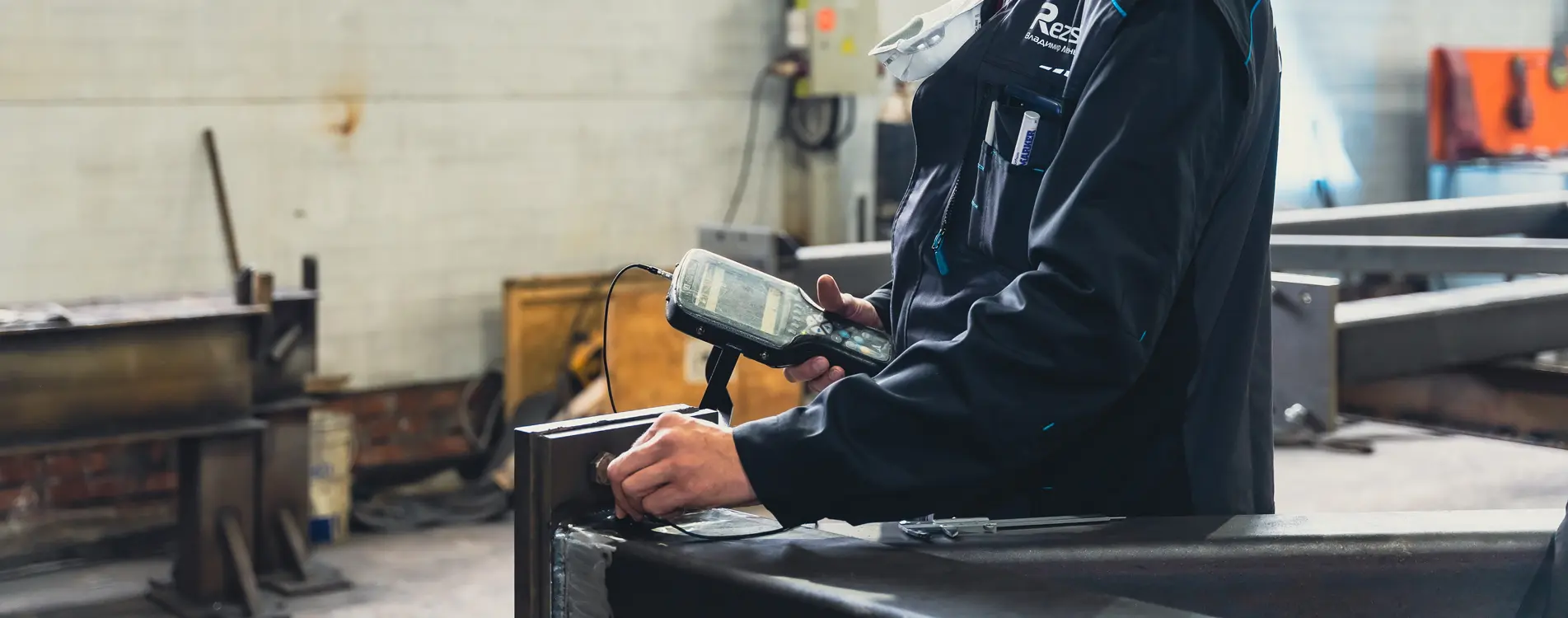
QUALITY CONTROL
The laboratory of nondestructive inspection is a guideline for safety in compliance with the rules and requirements.
Quality control at the Reztsoff metal structure plant comprises:
- certified employees with qualification certificates and admitted as specialists of nondestructive inspection;
- certified and verified equipment and tools;
- methods of visual, measuring, ultrasonic and radiation monitoring;
- management of regulatory technical documentation.
Quality control is performed taking into account:
- requirements of design and regulatory documentation;
- functional purpose of metal structures;
- manufacturing technologies;
- conditions of construction and operation;
- level of responsibility.
We control the quality of:
- materials at the stage of acceptance, storage and preparation for cutting;
- details cutting and machine processing;
- holes for bolted connections;
- blanks made of sheet and profile rolled products;
- intermediate, control and general assembly;
- welding joints;
- marking of metal structures;
- anticorrosive protection.
CONTROL METHODS AT REZTSOFF PLANT
VISUAL INSPECTION
It is the simplest and fastest method, and at the same time, a highly effective means for preventing and detecting defects. It is basic and only after it other methods of nondestructive inspection (ultrasonic testing, magnetic testing, etc.) are applied.
Visual inspection is regulated by the instruction on visual and measuring control RD 03-606-03, which contains the requirements for personnel qualification, recording of results, control means, control process and assessment methods.
Visual and measuring inspection is carried out with simple tools using a task list.
ULTRASONIC FLAW DETECTION (UT)
Ultrasonic flaw detection is a method of monitoring and searching for hidden defects in a material by emitting and accepting ultrasonic vibrations reflected from internal discontinuities (defects), and further analysis of their amplitude, arrival time, shape and other characteristics using special equipment – an ultrasonic flaw detector.
UT is effective in searching for air voids, heterogeneity of chemical composition (slag inclusions) and detection of non-metallic elements.
Welds are the most widespread application of ultrasonic flaw detection. This is achieved due to the mobility of the ultrasonic installation, high control efficiency, high accuracy as well as high sensitivity to any internal and surface defects of welds.
X-RAY FLAW DETECTION
It is designed to detect hidden defects in welded joints.
This method is based on the absorption of X-rays, depending on the density of the medium and the atomic set of elements that form the material of the medium. In the presence of defects, the rays passing through the metal are attenuated to varying degrees. The intensity of the transmitted rays allows to determine the location and presence of metal inhomogeneities.
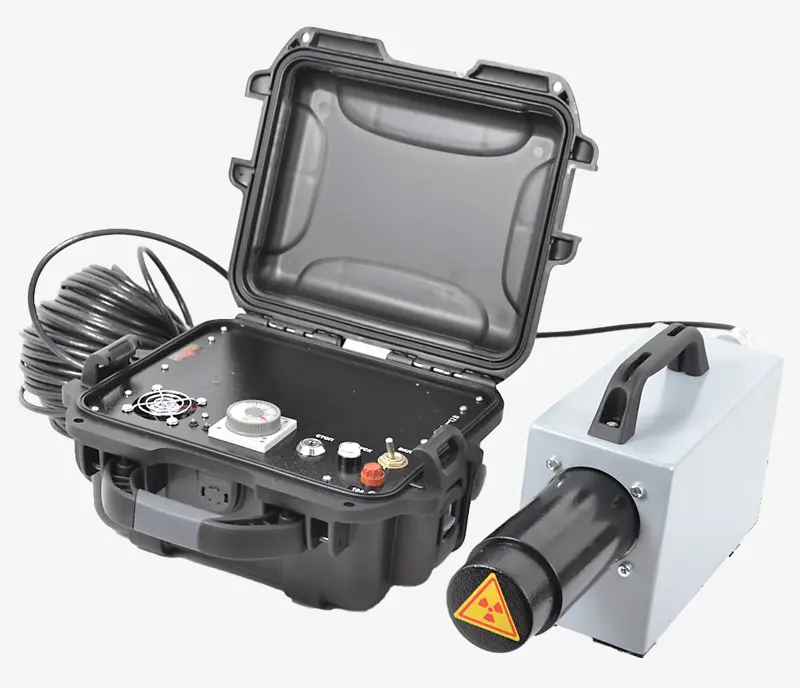
CONTROL STAGES
INCOMING INSPECTION OF MATERIALS
Acceptance inspection of incoming goods is an important stage of production. This type of inspection is performed at the plant. The main goal is to prevent the launch of products that do not comply with the requirements of the metal construction and structural engineering drawings.
At this stage we check:
- compliance of data in shipping documents with the quantity of received rolled products;
- availability of certificates for rolled metal (validity period, batch number, melting number, chemical composition, mechanical properties, etc.),
- marking of rolled metal;
- wall thickness of shaped pipes, rolled sheets, I-beams, channels;
- diameter and sides of shaped pipes;
- dimensions of channel walls, I-beams and angles;
- height of I-beams, channels and other types of rolled products.
OPERATIONAL CONTROL
Operational control is conducted with the compliance of the manufacturer’s documentation. The selected details from one batch are examined, defects are detected, the configuration of all parts of the design documentation is checked, the quality of the assembly, the reliability of bolted connections etc., is assessed.
One of the most important stages of operational control is assembly control, which ensures the quality of assembly of metal structures during the installation stage. At this stage, we check the geometry (geometric dimensions according to the structural engineering drawings, perpendicular alignment of the structure, diameter of the holes), as well as the quality of the assembly for high-quality welding: for this we perform a control assembly.
ACCEPTANCE INSPECTION
Acceptance control is to be performed at handover of each batch of metal structures and their elements. Both the entire batch and individual elements can be tested.
In this case the following is checked:
- quality of welded joints;
- anticorrosive coating;
- compliance with the configuration and technical parameters of the project;
- labeling.
Testing works are carried out by specialists of our laboratory of nondestructive inspection.
EQUIPMENT
At the quality control stage we use the following tools:
- a set for visual and measuring control;
- “MASTER” ultrasonic A1212 flaw detector;
- ultrasonic A1209 thickness meter;
- Arina-3 X-ray flaw detector.
Based on the results of the laboratory tests, a conclusion confirming the quality of welded joints is issued.
